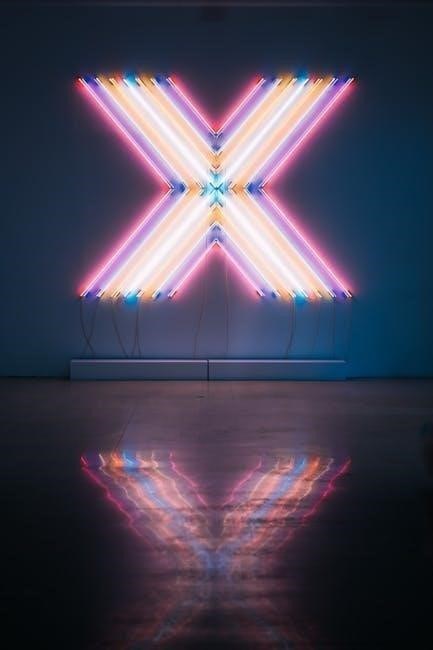
Hard manual work involves physically demanding tasks requiring strength, endurance, and skill, often in industries like construction, manufacturing, and agriculture, where human effort is essential.
Definition of Hard Manual Work
Hard manual work refers to physically demanding tasks that require significant strength, endurance, and hands-on effort. These jobs often involve repetitive motions, heavy lifting, and working in challenging environments. Unlike automated or desk-based roles, manual labor relies heavily on human physical exertion rather than machinery. Examples include construction, farming, and factory work, where workers engage in activities like lifting, carrying, and assembling materials. Manual labor jobs can be skilled or unskilled, depending on the role, but they all share a common trait: the need for physical stamina and the ability to perform tasks that machines cannot easily replicate. This type of work is essential in industries where human dexterity and adaptability are crucial, making it a cornerstone of many economies worldwide.
Importance of Manual Labor in Various Industries
Manual labor is indispensable across numerous industries, ensuring the production and delivery of essential goods and services. In construction, workers lay foundations, assemble structures, and install systems, forming the backbone of urban development. Manufacturing relies on manual labor for assembly lines, quality control, and machinery operation, driving global supply chains. Agriculture depends on farmers and harvesters to cultivate and gather crops, feeding populations worldwide. Even in sectors like healthcare and transportation, manual roles such as orderlies and delivery workers play vital parts. Without manual labor, critical infrastructure, consumer goods, and food production would grind to a halt, emphasizing its irreplaceable role in sustaining modern society and economic growth. Its contributions remain fundamental to industry operations and societal well-being.
Categories of Hard Manual Work
Hard manual work is categorized into unskilled, skilled, and specialized roles, each requiring varying levels of expertise and physical effort to execute tasks effectively across industries.
Unskilled Manual Labor Jobs
Unskilled manual labor jobs require minimal training and expertise, often involving repetitive or physically demanding tasks such as factory work, warehouse duties, or general construction assistance. These roles are typically entry-level, providing opportunities for individuals to gain experience and build foundational skills. Despite the lack of formal qualifications, these jobs are essential in industries like manufacturing, agriculture, and logistics, where manual handling of goods, materials, and equipment is necessary. Workers in these roles often develop physical endurance and adaptability, which are valuable for career advancement. Many unskilled laborers start here and later transition into skilled trades or supervisory positions, demonstrating the potential for growth within this category.
Skilled Manual Labor Jobs
Skilled manual labor jobs require specific training, certifications, or experience, often involving specialized tasks such as plumbing, electrical work, or welding. These roles demand a higher level of expertise compared to unskilled labor, ensuring precision and quality in industries like construction, manufacturing, and healthcare. For instance, electricians and HVAC technicians must complete apprenticeships or vocational programs to master their trades. These jobs often involve problem-solving and adapting to unique situations, making them both challenging and rewarding. Skilled laborers typically earn higher wages and have clearer career advancement opportunities, such as moving into supervisory or leadership roles. Their work is crucial for maintaining infrastructure, ensuring safety, and driving productivity across various sectors. These roles highlight the importance of combining physical effort with technical knowledge to achieve successful outcomes.
Specialized Manual Labor Roles
Specialized manual labor roles require unique expertise and often involve niche tasks that demand advanced skills. These roles are typically found in industries like telecommunications, aerospace, or healthcare, where precision and technical knowledge are paramount. For example, lineman in telecommunications climb tall structures to maintain power lines, while surgical instrument technicians sterilize and prepare medical tools. These jobs often necessitate certifications, licenses, or extensive on-the-job training. Specialized laborers work in high-stakes environments, ensuring safety and efficiency in critical operations. Their contributions are vital to maintaining essential services and infrastructure, making them indispensable in modern society. These roles combine physical effort with specialized knowledge, underscoring the diversity and complexity of manual labor in various sectors. The demand for such expertise continues to grow, offering stable and rewarding career opportunities for those willing to invest in their skills. These positions highlight the evolving nature of manual work in specialized fields.
Examples of Hard Manual Labor Jobs
Construction workers, factory workers, farmers, and harvesters are prime examples of hard manual labor jobs, requiring physical strength and endurance to perform demanding tasks effectively.
Construction Workers
Construction workers are a prime example of individuals engaged in hard manual work, often facing physically demanding tasks in challenging environments. Their roles involve lifting heavy materials, operating machinery, and performing tasks at heights, which require significant strength and endurance. Construction work is not only physically taxing but also mentally challenging, as it demands attention to safety protocols and precision in executing tasks. Workers often labor in extreme weather conditions, adding to the difficulty. Despite the challenges, construction workers play a crucial role in building infrastructure, making their contributions invaluable to society. Their work exemplifies the resilience and dedication required in hard manual labor jobs, highlighting the importance of physical and mental stamina in this field.
Factory Workers
Factory workers are integral to manufacturing and production processes, often engaging in hard manual work that involves repetitive tasks, heavy lifting, and operating machinery. Their roles typically require endurance, as they work long shifts in fast-paced environments. Many factory jobs involve handling materials, assembling products, and ensuring quality control, which can be physically demanding. Despite the lack of formal education required for some positions, factory workers must develop specific skills to perform their duties efficiently. The work environment can be challenging, with exposure to noise, machinery hazards, and strict deadlines. Factory workers play a vital role in producing goods, making their contributions essential to various industries. Their work showcases the blend of physical effort and attention to detail required in manual labor roles within industrial settings.
Farmers and Harvesters
Farmers and harvesters are essential to agriculture, engaging in hard manual work that involves planting, cultivating, and harvesting crops. Their roles demand physical stamina, as they often work long hours in unpredictable outdoor conditions. Tasks include operating machinery, handling tools, and manually picking produce, which can be labor-intensive. Farmers must also manage land, monitor crop health, and adapt to seasonal changes, requiring a mix of physical effort and strategic planning. Despite the challenges, farming is a rewarding profession that ensures food production and sustains local economies. Harvesters, in particular, face time-sensitive work during peak seasons, often working tirelessly to meet deadlines. Their contributions highlight the importance of manual labor in maintaining food security and supporting communities worldwide.
Physical and Mental Challenges
Engaging in hard manual work exposes individuals to physical strain, health risks, and mental stress, highlighting the human cost behind essential labor.
Physical Strain and Health Risks
Hard manual work often leads to physical strain, with repetitive tasks and heavy lifting causing musculoskeletal disorders and injuries. Prolonged exposure to demanding environments can result in long-term health issues, such as chronic pain or occupational diseases. Workers may face hazards like harmful fumes or ergonomic risks, which can exacerbate physical fatigue. The bodily toll of such labor is evident in the higher rates of workplace injuries compared to other professions. Additionally, the cumulative effect of years of physical exertion can lead to premature wear on joints and muscles, further complicating health outcomes. These risks underscore the importance of proper safety measures and regular health monitoring for those engaged in manual labor.
Mental Fatigue and Stress
Engaging in hard manual work often leads to mental fatigue and stress due to the high physical demands and repetitive nature of tasks. Workers in industries like construction and manufacturing frequently experience emotional strain from long hours, tight deadlines, and the pressure to maintain productivity. The monotony of certain roles can contribute to a sense of burnout, while the physical exhaustion further exacerbates mental tiredness. Additionally, the lack of control over workload or unpredictable working conditions can heighten stress levels. Mental fatigue may impair concentration, increasing the risk of accidents and reducing overall job performance. These challenges highlight the need for employers to implement stress management programs and provide mental health support to workers in manual labor roles.
Workplace Hazards and Safety Concerns
Hard manual work often exposes individuals to significant workplace hazards, posing serious safety concerns. Physical risks include injuries from heavy lifting, falls from heights, and accidents involving machinery. Environmental factors, such as exposure to harmful substances or extreme temperatures, can further endanger workers. Jobs like roofing or construction involve working at heights, increasing the likelihood of fatal accidents. Additionally, repetitive tasks can lead to long-term health issues, such as musculoskeletal disorders. Employers must prioritize safety protocols, including proper training, protective equipment, and regular inspections of equipment and workspaces. Despite these measures, the inherent dangers of manual labor highlight the need for continuous vigilance and adherence to safety regulations to protect workers from preventable harm and ensure a safer working environment.
Career Paths in Manual Labor
Manual labor offers diverse career paths, from entry-level positions to skilled trades requiring certifications, and opportunities for advancement into supervisory or leadership roles.
Entry-Level Positions
Entry-level manual labor positions provide foundational experience for those new to the field, often requiring minimal qualifications but offering on-the-job training to build essential skills. These roles include general laborers, warehouse workers, and assistants in various industries. They involve tasks such as material handling, cleaning, and basic tool operation, which help individuals develop physical stamina and work ethic. Many entry-level positions serve as stepping stones to more specialized or skilled trades, allowing workers to progress in their careers. Employers often prioritize reliability and willingness to learn over formal education, making these roles accessible to a wide range of individuals.
Skilled Trades and Certifications
Skilled trades and certifications represent a significant step up from entry-level positions, requiring specialized knowledge and expertise. These roles, such as electricians, plumbers, and HVAC technicians, demand formal training or apprenticeships to master specific skills. Certifications, often obtained through trade schools or professional organizations, validate an individual’s competency and commitment to their craft. For instance, a plumber may earn a state license after completing an apprenticeship, while an electrician might obtain certifications in safety standards or specific electrical systems. These credentials not only enhance job prospects but also lead to higher pay and greater respect in the industry. Transitioning from general labor to skilled trades often involves dedication to continuous learning and a willingness to invest time in professional development, making these roles a cornerstone of career advancement in manual labor fields.
Supervisory and Leadership Roles
Supervisory and leadership roles in manual labor represent the pinnacle of career advancement, where individuals transition from hands-on work to guiding and managing teams. These roles require strong communication, organizational, and problem-solving skills, as supervisors oversee projects, ensure safety protocols, and maximize efficiency. Often, these positions are filled by experienced workers who have risen through the ranks, demonstrating leadership potential and a deep understanding of the trade. For example, a construction foreman or crew leader directs workers, coordinates tasks, and ensures project timelines are met. These roles demand a blend of technical knowledge and interpersonal skills, as supervisors must motivate teams, resolve conflicts, and make strategic decisions. Leadership positions offer higher pay, greater responsibility, and the opportunity to mentor others, making them a rewarding goal for those in manual labor careers.
The Future of Manual Labor
The future of manual labor involves balancing technological advancements with human skill, as automation transforms industries while creating demand for adaptability and specialized expertise, driving the evolution of roles and the need for continuous learning to stay competitive.
Impact of Automation and Technology
Automation and technology are reshaping manual labor, with machines increasingly handling repetitive and physically demanding tasks. While this reduces the need for certain jobs, it also creates demand for skilled workers to operate and maintain advanced systems. For instance, robotic assembly lines in factories have replaced traditional manual labor, but they require technicians to oversee their operations. Similarly, in construction, automated tools improve efficiency but necessitate workers with technical expertise. Despite these changes, manual labor remains essential for tasks requiring human precision and adaptability. The integration of technology, however, underscores the need for continuous learning and upskilling to remain relevant in evolving industries. This shift is expected to redefine roles, blending physical work with technological proficiency, ensuring that manual labor adapts to the modern workplace while retaining its core value. The balance between automation and human effort will likely shape the future of these jobs.
Changing Job Market and Demand
The job market for manual labor is evolving, with a noticeable shift toward skilled trades and specialized roles. While automation reduces demand for unskilled jobs, there is a growing need for workers with specific expertise, such as electricians, plumbers, and HVAC technicians. Young professionals, including college graduates, are increasingly transitioning from white-collar positions to manual labor, seeking stability and hands-on fulfillment. This trend reflects a broader recognition of the value of physical work in sustaining industries like construction, manufacturing, and agriculture. Despite these changes, manual labor remains a cornerstone of the global economy, particularly for roles requiring human dexterity and adaptability. The demand for skilled manual workers is expected to persist, even as technology advances, ensuring that these jobs remain vital and in demand for the foreseeable future.
Evolution of Skills and Training
The evolution of skills and training in manual labor reflects the changing demands of industries and technological advancements. Traditionally, manual labor relied heavily on physical strength and basic tools, but modern roles now require specialized skills and certifications. On-the-job training is increasingly supplemented by formal education and apprenticeships, ensuring workers are equipped with advanced techniques and safety protocols. For instance, construction workers now often learn to operate machinery, while factory workers may gain expertise in automated systems. Additionally, there is a growing emphasis on continuous learning, as industries adapt to new technologies and materials. This shift underscores the importance of adaptability and lifelong skill development for those engaged in hard manual work, ensuring they remain competitive and capable in a rapidly changing job landscape.
Personal Stories and Experiences
Personal stories reveal the physical challenges and emotional resilience of those in manual labor, showcasing journeys of skill mastery and personal growth through perseverance and fulfillment.
Young Professionals Transitioning to Manual Labor
Increasingly, young professionals are trading high-pressure white-collar roles for manual labor, seeking fulfillment in hands-on work. Many, like Ms. Liu in China, find purpose in physical tasks, valuing tangible results over office stress. Despite challenges like physical strain and skill development, they embrace the transition, often discovering personal growth and satisfaction in their new roles.
Challenges Faced by Long-Term Manual Workers
Long-term manual workers often face significant physical and mental challenges. Prolonged exposure to demanding tasks can lead to chronic health issues, such as musculoskeletal disorders and long-term physical damage. Mental fatigue and stress are also common, exacerbated by the repetitive nature of the work. Workplace hazards, like invisible fumes or unsafe conditions, further exacerbate these risks. Additionally, the rise of automation and technological advancements threaten job stability, forcing workers to adapt or risk displacement. Many struggle with the emotional toll of transitioning to new roles or industries, highlighting the need for robust support systems and safety protocols to protect their well-being. Despite these obstacles, their resilience and dedication remain vital to many industries.
Success Stories and Career Growth
Many individuals in manual labor roles have achieved remarkable career growth and success. For instance, construction workers have advanced to supervisory roles or started their own contracting businesses. Similarly, factory workers have moved into quality control or management positions after gaining experience. In skilled trades, certifications in areas like plumbing or electrical work have opened doors to higher-paying jobs and entrepreneurial opportunities. Some manual laborers have transitioned into specialized roles, such as HVAC technicians or welders, where demand and compensation are high. These success stories highlight the potential for career advancement through skill development, hard work, and dedication. They prove that manual labor can serve as a foundation for long-term professional growth and financial stability, especially when combined with continuous learning and adaptability.
Tips for Succeeding in Manual Labor Jobs
Building physical endurance, improving work efficiency, and maintaining a healthy work-life balance are essential for thriving in manual labor roles, ensuring long-term success and well-being.
Building Physical Endurance
Building physical endurance is crucial for those in hard manual work, as it enables them to handle demanding tasks over extended periods. Regular exercise, such as strength training and cardio, helps improve stamina and reduce fatigue. Proper nutrition plays a vital role, ensuring the body is fueled with adequate proteins, carbohydrates, and nutrients to sustain energy levels throughout the day. Additionally, getting sufficient rest and sleep is essential for muscle recovery and overall physical resilience. Gradually increasing workload and incorporating stretching routines can also prevent injuries and enhance endurance. By prioritizing physical health, workers can perform more efficiently and safely in their jobs.
Improving Work Efficiency
Improving work efficiency in hard manual labor requires a combination of skill, organization, and focus. Workers should prioritize tasks, use tools effectively, and minimize unnecessary movements to conserve energy; Time management is key, as breaking tasks into smaller, manageable steps helps maintain momentum and reduces fatigue. Additionally, staying hydrated, taking short breaks, and maintaining a positive mindset can enhance productivity. Employers can also contribute by providing proper training and ensuring workers are well-equipped with the right tools. By adopting these strategies, manual laborers can complete tasks more efficiently, reduce errors, and achieve better overall results without compromising safety or quality.
Maintaining Work-Life Balance
Maintaining work-life balance is crucial for those engaged in hard manual labor to prevent burnout and ensure overall well-being. Setting clear boundaries between work and personal time is essential, as manual labor can be physically and mentally exhausting. Allocating time for hobbies, family, and relaxation helps recharge energy levels. Engaging in regular exercise or meditation can improve mental health and reduce stress. Prioritizing rest and avoiding overtime when possible are vital to sustain long-term balance. Communicating with employers about workload and seeking support from colleagues or supervisors can also help manage demands. By balancing work responsibilities with personal interests and self-care, manual laborers can maintain their physical and mental health while enjoying a fulfilling life outside of work.
Hard manual work remains vital to society, requiring strength, resilience, and dedication. Despite challenges, it fosters personal growth and contributes significantly to economic and societal progress.
The Value of Hard Manual Work in Society
Hard manual work is foundational to society, supporting industries like construction, manufacturing, and agriculture. Workers in these roles build infrastructure, produce goods, and ensure food security; Despite physical and mental challenges, their efforts sustain economic stability and community well-being. Often overlooked, manual labor is vital for maintaining daily life, from roads to consumer products. These jobs create employment opportunities and contribute significantly to GDP. Recognizing their importance fosters respect and support for improving working conditions and valuing their role in societal progress.
Encouraging the Next Generation
Encouraging young people to pursue manual labor careers is crucial for maintaining workforce vitality. Highlighting the stability and fulfillment these roles offer can attract new talent. Emphasizing opportunities for skill development and career growth, such as apprenticeships or certifications, can make these jobs more appealing. Sharing success stories of young professionals who transitioned to manual labor and found personal and financial growth can inspire others. Additionally, promoting better working conditions, safety standards, and fair wages is essential to attract the next generation. Encouraging schools to include trade education and partnering with industries to create entry-level programs can also help bridge the gap. By showcasing the value and dignity of hard manual work, society can inspire young individuals to embrace these vital roles and ensure a sustainable future for these industries.