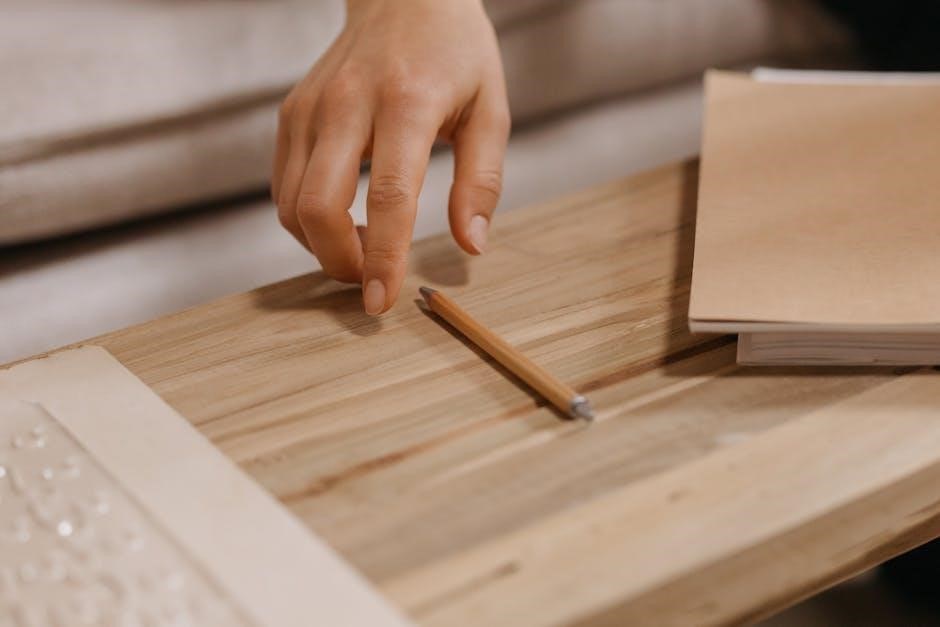
A manual lift table is a versatile tool designed to adjust the height of objects or people, enhancing workflow efficiency in various industrial and medical settings.
1.1 Definition and Purpose
A manual lift table is a device designed to raise or lower objects or individuals to specific heights, providing ergonomic solutions in industrial, medical, and manufacturing environments. Its primary purpose is to enhance workflow efficiency by allowing easy height adjustment, reducing physical strain, and improving safety. Commonly used for tasks like material handling, medical procedures, and workstation adjustments, these tables are essential for optimizing productivity and minimizing risks associated with manual lifting. By enabling smooth height transitions, manual lift tables play a crucial role in creating safer and more efficient workspaces across various industries.
1.2 Brief History and Evolution
The concept of manual lift tables dates back to the late 19th century, when basic mechanical lifting devices were first introduced to assist in industrial settings. Early designs were simple, relying on manual cranks or levers to raise and lower loads. Over the 20th century, advancements in hydraulic and pneumatic technologies led to more efficient and user-friendly designs. By the mid-20th century, hydraulic lift tables became widespread, offering smoother operation and greater load capacity. Modern versions incorporate electric and pneumatic systems, with a focus on ergonomics and safety. This evolution reflects the growing need for efficient, adaptable, and safe lifting solutions across various industries.
Key Features of Manual Lift Tables
Manual lift tables feature ergonomic designs, adjustable height settings, and robust construction, ensuring safe and efficient lifting in various industrial and medical environments.
2.1 Lifting Mechanism
Manual lift tables utilize either hydraulic or mechanical systems to raise and lower loads. Hydraulic systems provide smooth, precise height adjustment, often with foot pedals for hands-free operation. Mechanical systems, such as screw-driven or scissor lifts, offer simplicity and reliability. Both mechanisms ensure safe and controlled movement, minimizing strain during lifting tasks. Regular maintenance is essential to maintain optimal performance and safety. These mechanisms are designed to handle various load capacities, making them suitable for industrial, medical, and warehouse environments. The choice of mechanism depends on specific application needs, load requirements, and user preferences. Proper operation ensures efficient and ergonomic material handling.
2.2 Load Capacity and Weight Limits
Manual lift tables are designed with specific load capacities and weight limits to ensure safe and efficient operation. These limits vary by model but typically range from 500 to 5,000 pounds, depending on the intended use. Exceeding the maximum weight capacity can lead to equipment failure or safety hazards. It is crucial to select a lift table that matches the expected workload to maintain reliability and performance. Manufacturers provide detailed specifications, including weight limits, to guide users. Adhering to these guidelines is essential for optimal functionality and workplace safety. Proper load distribution and regular maintenance also play a role in ensuring the lift table operates within its designated weight range.
2.3 Height Adjustment Range
Manual lift tables offer a variable height adjustment range, typically spanning from 12 to 60 inches, depending on the model. This range allows users to position the platform at optimal heights for specific tasks, ensuring ergonomic workflows. The minimum and maximum heights are critical factors, as they determine the table’s versatility in different settings. Adjustable height settings enable efficient loading, unloading, and transferring of materials or equipment. Customizable options may also be available to suit particular workplace requirements. The height adjustment range is a key feature that enhances productivity, safety, and comfort in industrial, medical, and other applications. Proper height alignment reduces strain and improves operational efficiency.
2.4 Platform Size and Material
Manual lift tables feature platforms constructed from durable materials such as steel, aluminum, or stainless steel, ensuring strength and longevity. Platform sizes vary widely, ranging from compact designs for small loads to larger surfaces for heavy or bulky items. The material selection often depends on the intended application, with stainless steel being ideal for medical or food-grade environments. The platform’s size and material directly impact its load capacity, stability, and suitability for specific tasks. Customizable options may allow users to tailor the platform to their needs, ensuring optimal performance and safety. The design prioritizes durability, ergonomics, and ease of use, making it adaptable to various industries.
Applications of Manual Lift Tables
Manual lift tables are essential in industrial, manufacturing, warehouse, and medical settings, optimizing workflows by adjusting heights for tasks like assembly, storage, and patient care efficiently.
3.1 Industrial and Manufacturing Settings
Manual lift tables are indispensable in industrial and manufacturing environments, where they enhance workflow efficiency by enabling precise height adjustments for assembly lines, workstations, and material handling. These tables reduce physical strain on workers by allowing ergonomic positioning of heavy machinery or components. They are widely used for tasks such as welding, assembly, and quality control, ensuring optimal working heights to improve productivity. Their durability and reliability make them suitable for demanding industrial conditions. Additionally, customization options allow businesses to tailor lift tables to specific manufacturing needs, further streamlining operations and ensuring safety in the workplace.
3.2 Warehouse and Logistics
Manual lift tables play a crucial role in warehouse and logistics operations by streamlining material handling processes. They are used to load, unload, and transport goods efficiently, reducing physical strain on workers. These tables are ideal for ergonomically adjusting the height of pallets, crates, or other items, ensuring safe and comfortable working conditions. In logistics, they facilitate quick transfers between different levels, such as from trucks to storage areas, enhancing overall workflow. Their portability and durability make them suitable for demanding warehouse environments, where they help minimize workplace injuries and improve operational efficiency. This makes them an essential tool for optimizing logistics and supply chain management.
3.3 Medical and Healthcare Facilities
Manual lift tables are indispensable in medical and healthcare facilities, where they are used to safely lift and position patients, equipment, or supplies. They are designed to reduce physical strain on healthcare workers, promoting ergonomics and minimizing the risk of injuries. These tables often feature smooth, controlled movements to ensure patient comfort during transfers or procedures. In addition, their height adjustability allows for customization to suit various medical tasks, such as examinations or surgeries. Many models are constructed with easy-to-clean surfaces, making them suitable for sterile environments. By enhancing efficiency and safety, manual lift tables play a vital role in improving patient care and operational workflows in healthcare settings.
Safety Considerations
Manual lift tables require careful operation to ensure safety. Always follow load capacity limits and use emergency stop mechanisms. Regular maintenance is essential to prevent accidents.
Proper training and adherence to safety guidelines are critical for safe operation in any setting.
4.1 Safety Features and Precautions
Manual lift tables are equipped with essential safety features to ensure safe operation. Load capacity limits must never be exceeded to prevent structural damage or collapse. Emergency stop mechanisms are often integrated to halt operations immediately in case of an emergency. Regular maintenance of hydraulic cylinders, lifting mechanisms, and controls is critical to maintain reliability. Proper training and adherence to usage guidelines are mandatory to minimize risks; Overloading should be strictly avoided, as it can lead to equipment failure. Ensuring the table is placed on a stable, even surface is vital for optimal performance and safety. Always follow manufacturer instructions to prevent accidents and ensure compliance with safety standards.
4.2 Emergency Stop Mechanisms
Emergency stop mechanisms are critical components of manual lift tables, designed to immediately halt operations in urgent situations. These mechanisms, often in the form of easily accessible buttons or foot pedals, ensure rapid response to potential hazards. They are typically located on control panels or remotes for quick activation. Once engaged, the system should stop the lifting process instantly and render the table inoperable until manually reset; Regular inspection of these mechanisms is essential to ensure their functionality. Proper installation and maintenance of emergency stops are vital to prevent accidents and protect both operators and equipment. Compliance with workplace safety standards is mandatory.
Maintenance and Repair
Regular maintenance of manual lift tables includes lubricating moving parts, inspecting hydraulic systems, and cleaning surfaces to ensure smooth operation. Addressing repairs promptly prevents major breakdowns.
5.1 Regular Maintenance Tips
Regular maintenance of manual lift tables is essential to ensure optimal performance and longevity. Start by lubricating all moving parts to reduce friction and wear. Inspect hydraulic systems for leaks or damage, and clean surfaces to prevent debris buildup. Check the lifting mechanism for proper alignment and function. Tighten bolts and screws to maintain stability. Additionally, test the emergency stop mechanism to ensure it operates correctly. Finally, review user manuals for specific maintenance recommendations. Neglecting these steps can lead to safety issues or equipment breakdowns, emphasizing the importance of consistent upkeep.
5.2 Troubleshooting Common Issues
Common issues with manual lift tables often relate to mechanical or hydraulic malfunctions. If the table fails to lift, check for hydraulic leaks or insufficient fluid levels. Inspect the lifting mechanism for blockages or damage. A wobbling platform may indicate loose bolts or uneven weight distribution, requiring immediate tightening or rebalancing. Noisy operation could signal worn parts, such as bearings or gears, which need replacement. Always refer to the user manual for specific troubleshooting steps. If issues persist, contact a professional technician to ensure safety and proper functionality. Regular inspections can prevent these problems, minimizing downtime and extending equipment lifespan.
Design and Construction
Manual lift tables are built with durable materials like steel, featuring a sturdy frame and base for stability. They often include hydraulic systems for smooth height adjustment, customizable platforms, and mobility features like wheels for easy repositioning. Designs prioritize safety and efficiency, ensuring reliable performance in various environments.
6.1 Frame and Base Design
The frame and base of manual lift tables are constructed from durable materials, such as steel, to ensure stability and longevity. The base is typically wide to prevent tipping, while the frame is designed for structural integrity. Many models feature a reinforced base plate and a robust lifting column, which supports the platform securely. The frame is often powder-coated or treated for corrosion resistance, making it suitable for industrial environments. Some designs incorporate adjustable feet for leveling on uneven surfaces, enhancing stability. The overall construction prioritizes safety and durability, ensuring the lift table remains operational under heavy use.
6.2 Hydraulic vs. Mechanical Systems
Manual lift tables can operate using either hydraulic or mechanical systems, each offering distinct advantages. Hydraulic systems rely on fluid pressure to lift loads, providing smooth and precise height adjustment, especially for heavy-duty applications. They are ideal for industrial settings where stability and control are crucial. Mechanical systems, on the other hand, use screws, levers, or springs to elevate the platform, offering simplicity and lower maintenance. Hydraulic systems generally require more maintenance due to fluid checks and potential leaks, while mechanical systems are often quieter and more cost-effective. The choice between the two depends on the application, load capacity, and desired operational ease.
6.3 Customization Options
Manual lift tables can be customized to meet specific requirements, ensuring optimal performance in various settings. Common customizations include adjusting the platform size, height range, and load capacity to suit particular tasks. Additionally, materials and finishes can be tailored for durability in harsh environments or hygienic conditions, such as in medical facilities. Some models offer optional features like wheels for portability or ergonomic controls for ease of use. Customization options allow users to adapt the lift table to their unique workflows, enhancing efficiency and safety. This flexibility makes manual lift tables versatile tools for industries ranging from manufacturing to healthcare.
6.4 Portability and Mobility Features
Manual lift tables often feature portability and mobility enhancements, enabling easy relocation within workplaces. Many models include wheels or casters for smooth movement, while others offer lightweight designs for effortless transport. Some tables come with swivel casters for enhanced maneuverability in tight spaces. Additionally, certain models may include handles or grip points to facilitate manual movement. These features ensure that the lift table can be positioned precisely where needed, adapting to dynamic work environments. Portability is particularly beneficial in settings where tasks require frequent relocations, such as warehouses or medical facilities. Mobility enhancements make manual lift tables more versatile and user-friendly, optimizing workflow efficiency.
Market and Industry Trends
The manual lift table market is growing, driven by increasing demand for ergonomic solutions. Various types suit different needs, with technology advancements enhancing functionality and safety standards.
7.1 Types of Manual Lift Tables
Manual lift tables are available in various types to cater to different industrial and operational needs. Hydraulic lift tables are the most common, offering smooth height adjustment through a foot pedal or hand pump. Mechanical lift tables, on the other hand, rely on manual cranking or winch systems, providing a cost-effective solution for lighter loads. Pneumatic lift tables use compressed air for operation, ideal for clean environments. Additionally, scissor lift tables are popular for their stability and wide platform sizes, while portable lift tables are designed for mobility across workspaces. Custom lift tables can also be tailored to specific requirements, ensuring versatility in applications.
7.2 Factors Influencing Purchase Decisions
When selecting a manual lift table, several factors influence purchase decisions. Load capacity and height adjustment range are critical to ensure the table meets specific workload requirements. Platform size and material durability are also key considerations, as they impact functionality and longevity. Safety features, such as emergency stop mechanisms, are essential to prevent accidents. Portability and mobility options, like wheels or compact designs, are important for flexible workspace needs. Budget constraints often play a role, with buyers balancing cost against desired features. Additionally, brand reputation, warranty, and customer support are significant factors, as they ensure reliability and post-purchase assistance. Understanding these factors helps buyers make informed decisions tailored to their operational needs.
7.3 Emerging Technologies in Lift Tables
Emerging technologies are transforming manual lift tables, enhancing their functionality and safety. Integration of AI and IoT enables real-time monitoring and predictive maintenance, optimizing performance. Advanced control systems, such as AI-powered sensors, detect overload risks and auto-adjust heights for ergonomic efficiency. IoT connectivity allows remote monitoring, ensuring timely repairs and reducing downtime. Automation features, like smart foot pedals and touch controls, improve ease of use. Additionally, energy-efficient designs and eco-friendly materials are gaining traction, aligning with sustainability goals. These innovations not only modernize lift tables but also make them safer and more adaptable to diverse industrial needs, ensuring they remain vital tools in evolving workplaces.
Advantages and Limitations
Manual lift tables offer cost-effectiveness, safety, and ergonomic benefits but may lack the speed and capacity of powered models, requiring manual effort for height adjustments.
8.1 Benefits of Using Manual Lift Tables
Manual lift tables provide numerous advantages, including cost-effectiveness, ease of use, and ergonomic design, which reduces physical strain for operators. They are ideal for applications requiring precise height adjustment and are often more affordable than powered alternatives. Their compact design allows for efficient use of space in workshops or facilities. Additionally, manual lift tables promote workplace safety by enabling stable and controlled lifting, minimizing the risk of accidents. Regular maintenance is typically straightforward, ensuring longevity and reliability. These tables are versatile, catering to various industries, from manufacturing to healthcare, making them a practical and efficient solution for height adjustment needs.
- Cost-effective solution for height adjustment needs.
- Reduces physical strain with ergonomic design.
- Easy to operate and maintain.
- Versatile for multiple industrial applications.
8.2 Limitations and Drawbacks
Manual lift tables have certain limitations that may hinder their suitability for specific tasks; They often require manual effort, which can be physically demanding for operators, especially with heavy loads. Their load capacity is generally lower than powered lift tables, making them less ideal for heavy-duty applications. Additionally, manual lift tables may have limited height adjustment ranges and slower operation compared to hydraulic or electric models. They are also less portable for large-scale industrial use due to their weight and design. Furthermore, repetitive use can lead to wear and tear, requiring frequent maintenance to ensure optimal performance and safety.
- Requires physical effort, potentially straining operators.
- Limited load capacity compared to powered alternatives.
- Slower operation and limited height adjustability.
- Less portable and more maintenance-intensive.
Manual lift tables are essential tools for enhancing productivity and safety in various industries, offering versatility and efficiency. Despite limitations, ongoing innovations continue to improve their functionality and efficiency.
9.1 Summary of Key Points
Manual lift tables are essential tools for enhancing productivity and safety in various industries. They provide efficient height adjustment for objects or people, reducing physical strain and improving workflow. Designed with durability, these tables offer features like robust construction, customizable platforms, and advanced safety mechanisms. Applications span industrial, medical, and logistical settings, making them versatile solutions. Regular maintenance is crucial to ensure optimal performance and longevity. Despite their limitations, manual lift tables remain indispensable for ergonomic and efficient material handling. Emerging technologies promise further advancements, ensuring their continued relevance in modern workplaces.
9.2 Future Outlook and Innovations
The future of manual lift tables is poised for significant advancements, driven by emerging technologies and evolving industry needs. Integration of smart hydraulics and IoT connectivity is expected to enhance functionality, enabling real-time monitoring and improved safety. Ergonomic designs will continue to prioritize user comfort and efficiency. Additionally, sustainable materials and energy-efficient systems may become standard, aligning with global environmental goals. Customization options will likely expand, catering to specific industry requirements. These innovations will ensure manual lift tables remain indispensable in modern workplaces, offering cutting-edge solutions for material handling and workplace safety.